Project PREMANT
File
2022
Industry
Encore-lab, EMESA, Angel Ruiz Ibañez S.A
Dataloggers, sensors, DSS, interfaces.
Project description
Maintenance is a key element in any industrial process, regardless of the sector, as it contributes to reducing costs, enhancing quality and efficiency and avoiding accidents at work, among other advantages. Until not so long ago, corrective maintenance, based on the condition of equipment, was predominant in industry.
However, thanks to technological evolution, big data and digitalisation, maintenance strategies have become preventive and even predictive, gaining weight in Industry 4.0.
Technology in predictive maintenance, which is mainly based on digitalisation, is growing rapidly, and so are solutions in condition monitoring, which is one of its most important activities.
Today there is a great diversity in the application of condition measurement techniques, such as: vibration analysis, temperature measurement, speed, current monitoring and analysis, thermography, ultrasound, lubricant analysis, acoustic analysis, etc.
The general objective of the project is the implementation of a proof of concept of a new industrial process monitoring system for decision making related to predictive maintenance and unplanned maintenance and repair of equipment.
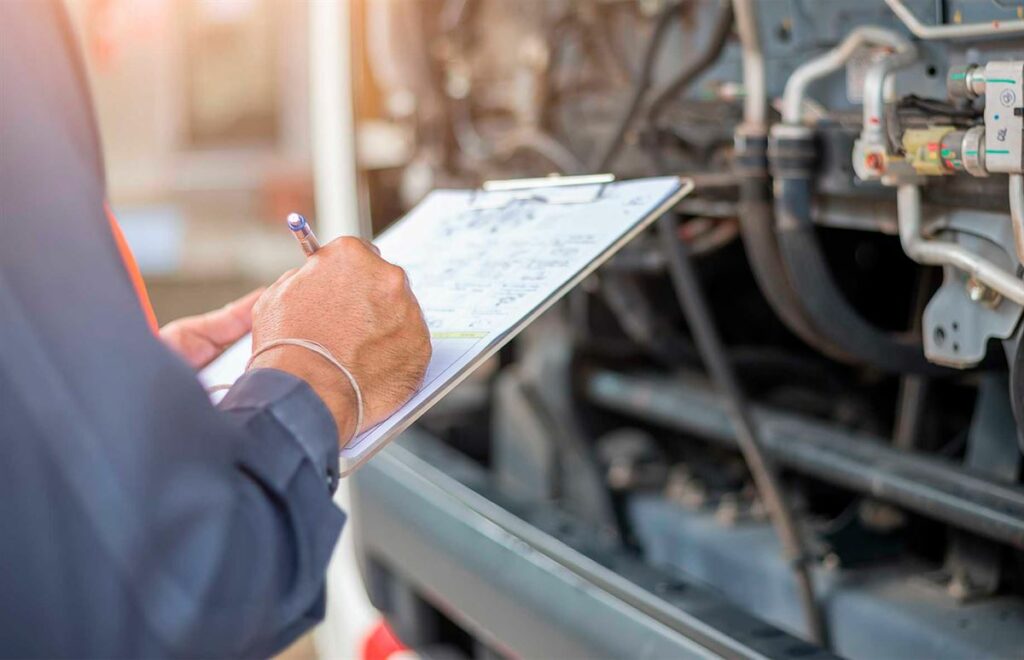
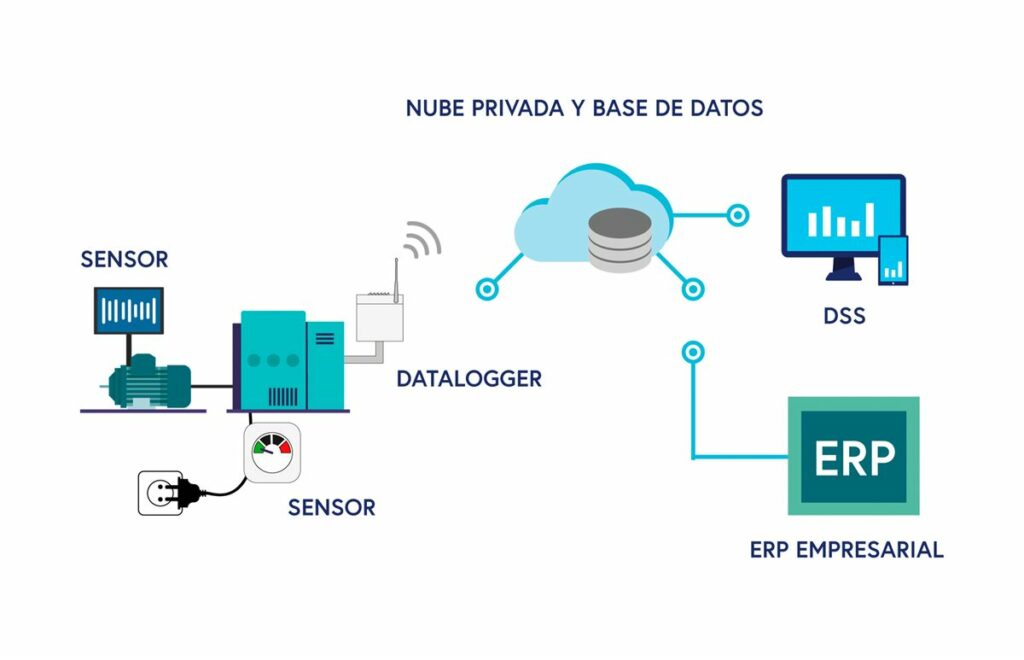
Reply from Encore-Lab
The project is based on the installation of scalable and sensor-agnostic dataloggers that send information to private repositories and are subsequently processed through a DSS.
The project also proposes access to this data and the management of the different assets through REST API interfaces.
Results
The project’s innovations focus on the following points:
- Use of energy consumption data. A lack of maintenance, apart from leading to machine breakdowns and unexpected stoppages, causes higher energy consumption during operating periods. This consumption is taken into account as a consequence in many maintenance analysis systems and is not used as a problem indicator, as machine energy efficiency systems make their analysis complex. PREMANT allows this data to be acquired through transducers installed on the machine or directly from the machine control systems so that it can be processed by future machine learning systems for early detection of anomalies in the operation.
- Connection with ERP systems. The aim is to develop a connection module between the backend of the private data repository and the company’s ERP. Having this information, either through indicators or through raw data, makes it easier for plant managers to make decisions regarding the allocation of manufacturing orders, prioritising them according to workload, material, delivery times and machine availability. It also allows maintenance departments to plan scheduled shutdowns or machine overhauls at appropriate times when the machine’s workload is reduced.
- There are many factors that come into play and determine the processes of the production chain. It is often difficult to have a global vision of the processes that are decisive for decision making without data and without taking into account the different areas of the company.
- It is often difficult to have a global vision of the processes that are decisive for decision making without data and without taking into account the different areas of the company.
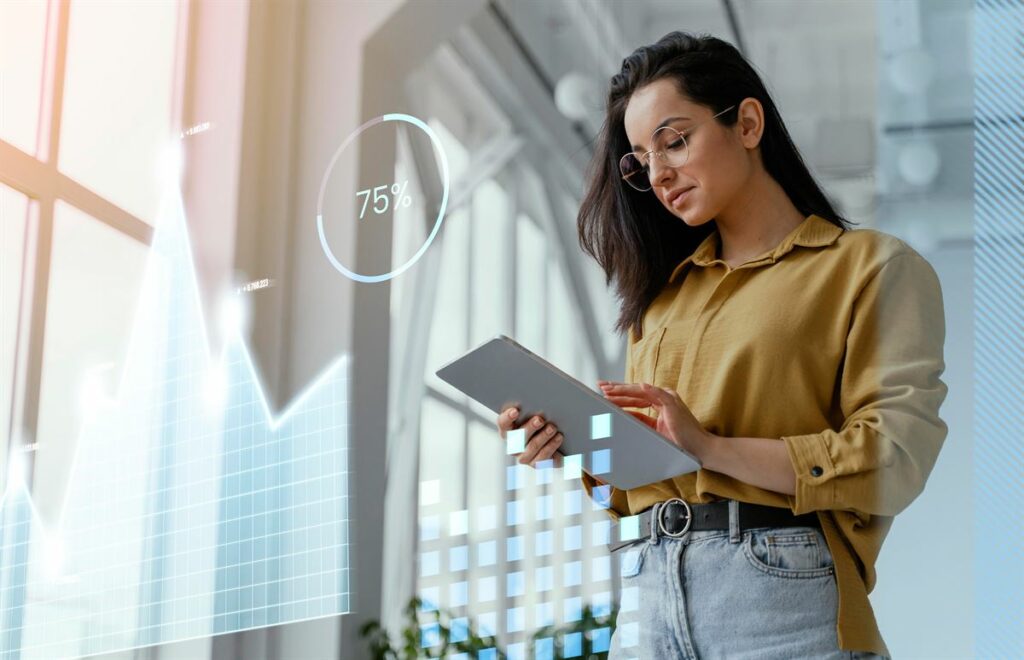